长期以来,染料及中间体生产行业一直难以摆脱人们印象中污染严重的形象,尤其是去年9月的腾格里沙漠污染事件,更是将染料及中间体行业推上环保的风口浪尖。而随着今年号称史上最严的新《环保法》实施,能否解决污染问题将对企业的生死存亡和行业发展产生深远影响。那么,长期困扰行业的污染之痛该如何根治?随着近年染料行业全球地位的转换和环保意识的提升,中国染料行业在环保方面又作出了哪些努力?
绿色发展,努力有目共睹
改革开放后,经过30多年与欧美及亚洲染料企业的激烈竞争,中国染料行业取得了产量和市场两大收获。染料产量占全球60%以上,市场份额占全球40%以上。然而,有收获就有牺牲。“我们付出了巨大代价,环保欠账太多,造成环境严重污染,这些不争的现实情况历历在目。欠账一定要还上,近几年行业一直在努力改变这一情况。”中国染料工业协会秘书长田利明说。
其实,染料行业的发展经历只是改革开放后我国经济高速发展的一个缩影。我国创造了30多年经济高速发展的伟大成就,但“环境红利”被透支,多年积攒的环境欠账在当前集中显现。在新常态下,中央不断传递出明确信息,就是宁可让发展速度降下来,也要转变发展方式,走生态环境与经济发展共赢的新道路。
在田利明看来,染料行业正是在走一条降增速提升发展质量的路子。笔者了解到,改革开放后,染料行业产量增速最高曾达到26.5%,但“十二五”以来,染料行业产量增速保持低于10%,较前些年明显减速。田利明认为,这恰恰说明了行业理性发展。最近一两年,染料价格大幅上涨,产量并没有大量增加,企业将更多利润投入到了技术研发和工艺改造中。“最近几年,染料行业利润率不断增长,这也给企业还清环保欠账提供了资金支持。并不是赚了钱以后大家愣着什么都不做,大家一直在朝着绿色发展的方向努力,在清洁生产和‘三废’治理方面进步还是很快的。”他强调说。
据介绍,近年来,国内企业自主研发出染颜料中间体加氢还原清洁生产制备技术、原浆干燥清洁生产制备技术等一批清洁生产技术。业内专家告诉笔者,有几项技术已经达到了较高的水平,在应用开发方面也已经达到了相当成熟的地步,国内技术与国际最先进的技术相比,已差距甚微。“五年前,重点企业里都有外国专家参与技术研发。现在外国专家少了,因为我们的技术先进了,所以人家不来了。”田利明说。
2010年,染颜料中间体加氢还原等清洁生产制备技术,染料膜过滤、原浆干燥清洁生产制备技术,有机溶剂替代水介质清洁生产制备技术,低浓酸含盐废水循环利用技术等4项技术被列入工信部《清洁生产技术示范和应用推广目录(第一批)》。据了解,这些技术目前有的已经得到普遍应用,有的还在推广阶段。比如染料膜过滤、原浆干燥清洁生产制备技术就已较为成熟,该技术从工艺源头做起实施染料合成全过程的清洁生产,目前,在染料总产量中有30%应用了这个技术,减少总废水量20%。
业内大型企业积极采用这些技术,建设清洁生产项目。自2011年起,杭州吉华集团、山西青山化工公司、浙江龙盛集团、河北华戈化工有限公司、浙江闰土集团、河南洛染股份有限公司等6家企业先后获得工信部、财政部清洁生产专项资金支持。通过清洁生产项目的建设,企业不仅自身取得了显著的节能减排效果,同时也促进了行业整体清洁生产水平的提升。
田利明说,近5年来,企业在环保治理方面投入了大量资金,排名前十的企业在环保方面的投资均超过亿元。这些资金主要用于“三废”治理、清洁生产工艺改造等方面,取得了良好效果。在多方共同努力下,行业环保治理取得了显著进步。染料工业协会的统计数据显示,近5年期间,入驻化工园区的生产企业占80%,产量占95%。通过各类清洁生产技术的开发应用,染料工业废水得到有效治理和控制,废水产生数量每年减少1500万~1800万吨,COD排放每年减少15~20吨。
湖北楚源集团有关负责人表示,环保是企业各项工作的重中之重。近5年,楚源已投入5亿多元用于环保治理,在高浓度废水的治理、“三废”的回收利用等方面取得了突破。目前,“三废”排放完全达标,“三废”的回收利用形成了一个完整的体系。企业主导产品H酸已开发出新的成熟的绿色工艺,大大减少了有机污染物和无机盐类的排放。
浙江龙盛集团有关负责人表示,近年来企业全面推行“一体化”清洁生产,重视研究开发和采用清洁生产的工艺技术,从根本上减少废物的产生量。同时,发挥产业链的规模效应、协同效应,实现资源优化配置,每年副产物回收及资源综合利用创造价值1亿元以上,余热回收及有效利用年节能折标煤2万吨以上。
在染料企业自身不懈努力的同时,国家也鼓励企业采用联合攻关的形式,促进清洁生产方面的创新。比如2010年,染料产业技术创新战略联盟在北京宣告成立。致力于染料行业清洁生产技术的创新开发和产业化是联盟的重要目标之一。2014年底,由该技术联盟承担的“十二五”国家科技支撑计划项目“染料及中间体清洁制备与应用关键技术开发”圆满结题。该项目由染料产业技术创新战略联盟内的24家企业联合攻关,开发出9个重要中间体清洁生产新技术、4种新印染工艺、染料废水处理及回收新技术开发等,共建立了23套示范工程。项目实施过程中已减少废水排放250多万吨/年,减少固体废弃物19.4万吨/年。中国石油和化学工业联合会专家认为,这些新技术的问世和示范项目的建设,使企业对于清洁生产、环保安全的重视比以往任何时候都有了显著提高。
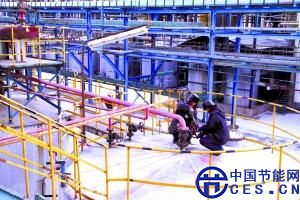
吉林石化染料厂通过尾气低温冷凝回收和催化氧化的先进工艺技术,对苯酚丙酮尾气中的有机物进行处理。
清洁生产,依然任重道远
尽管在业内企业的共同努力下,染料行业在环保方面取得了一些进步,但是一个不容回避的事实是,频发的环保事故仍然是行业之痛,阻碍着染料行业的健康持续发展。
在2014年被媒体曝光的腾格里沙漠污染事件中,宁夏明盛染化公司采用国家淘汰工艺进行染料中间体还原物生产,对“三废”并未进行有效处理,直排沙漠腹地。这样恶性污染事件的发生,带来了产品价格的大幅波动,扰乱了正常市场秩序。在一些环保监管较弱地区,很多企业绞尽脑汁逃避环保执法,同时依靠地方保护,以“游击化工厂”的方式存在,干扰市场,使依靠技术进步的企业得不到应有的利润回报,形成了劣币驱逐良币的局面,这也是行业面临的残酷现实。
正如业内专家所说,污染治理的根本出路在于开发与应用清洁工艺。既然目前国内相关技术的产业化已经成熟了,那为什么还是有一些企业不肯采用先进的技术,难道是因为存在技术壁垒?其实不然,田利明说,国家推行的清洁生产产业化技术,基本没有技术壁垒,即便是有些技术涉及到企业专利,也完全可以走专利有偿使用这个路子,只要企业愿意对此进行投资,都是可以实现的。
一位业内人士以还原物清洁生产工艺为例对此进行了说明,还原物清洁生产示范项目是一个国家项目,所得的成果行业共同拥有,所采用的清洁技术也基本为行业所了解,所以并不存在所谓的技术壁垒,同行完全可以自发地实现清洁生产。但新工艺与旧工艺相比,生产成本一定会高一些。再如催化加氢在染料中间体间苯二胺、邻苯二胺、对苯二胺、还原物等领域的应用都较成熟,浙江龙盛、四川红光、扬农化工和蓝丰化工都有着商业化的成功实践,但是铁粉还原、硫化碱还原等落后工艺仍然存在且被一些企业采用。可以说,问题的本质并不在于技术本身,而在于企业是否有意愿来应用清洁生产工艺和“三废”治理技术。
事实上,很多企业往往更倾向选择能为自己降低成本的技术,而对提升成本的技术则积极性较低。据悉,在清洁生产技术中,推广效果最好的原浆干燥清洁生产制备技术。目前只要具备条件能够应用这项技术的企业,基本都实施了工艺改造。因为采用这一技术可以缩短工艺降低成本,所以企业积极性比较高,都愿意做。但是连续硝化和催化加氢技术推广难度较大,因为技术含量高、设备复杂、投入很大,采用这一技术将会提高成本,所以很多企业不愿意做。
目前国家对于推行清洁生产技术,并没有强制性的措施,仅靠企业自律。在资金方面,仅有部分资金支持来鼓励企业进行清洁生产改造。对此,一位染料业界人士表示,虽然国家对于符合产业政策的企业有绿色信贷支持,但是政策较虚,并无太实际的意义。由于行业较小,针对染料的国家产业政策较少,所以有关的支持资金更少,支持范围有限。按理说,随着近几年染料及中间体产品价格的水涨船高,企业有了利润支撑,应该可以积极主动地去采用更清洁的生产工艺,然而遗憾的是,在很多环保监管较弱地区,企业在丰厚利润面前自律性也往往大打折扣。
除了自身问题,一些来自外部的因素左右企业的行为。此前,环保部门曾经想让企业上马催化加氢还原装置,但是竟然遭到当地安监部门以可能带来安全风险的理由反对。这种政府部门管理不科学、各自为政而出现监管矛盾的现象也说明,在环保升级这类重大问题上需要多方力量共同协作,不能将为企业提供帮助变为提供干扰。
田利明还表示,目前污染问题主要出现在非园区企业和一些小企业中。国内很多小企业与国外相比普遍存在发展不规范的问题,因此如何引导他们向大企业学习规范化经营是当前的重点。为此应加强行政干预,加大环保执法力度,并要打破地方保护。他相信,随着新环保法措施的落实,污染现象将会有明显改观。
痛定思痛,重症当下猛药
染料行业的环保形势未来会愈发严峻,这一观点已被业内人士所接受。目前国家尚未出台针对于染料工业的排污标准,但是农药、橡胶制品等精细化工行业都已出台行业排污标准。来自染料工业协会的消息称, 2009年染料工业排污标准就正式列入环保部的计划,但是出于多种原因,至今这一标准尚在酝酿之中。不过,业内人士也普遍认识到,一旦这样的标准出台,肯定会挤掉一批环保不达标企业的生存空间。
在业内人士看来,中国染料行业已经拥有了全球第一产能和与昔日不可同日而语的市场地位,产品利润也逐渐提升,如果在这样有利的情况下,还要污染、牺牲环境,的确有愧于业界良心。未来环保虽然是顶在头上的压力,但是企业更应该将压力化为契机,毕竟时代不同了,行业的形象也应该改变了。
不少企业说,环保投入,不投是等死,投了是找死。现在新环保法这么严格,不进行环保投入,肯定是没出路的。但是,如果上亿的资金投进去了,工艺技术改进了,可产品的生命力一旦没了,投资可能化为泡影,毕竟这不是改进产品的投资,再加上环保设施的运营费用也很高,所以说可能会是找死。但是,“找死有可能不死,等死一定会死。出路就在于此,不投一定死;投了虽然是找死,但是看准以后绝大多数都死不了。”田利明如是说。
事实上,很多大企业的经历很好地说明了这一点。业内人士透露,纵观大企业的发展历程,其实是从先污染后治理的路子走过来。10年前,无论是“三废”治理技术还是清洁生产技术,都不如现在先进,不仅很多企业都不具备处理“三废”的能力,甚至一些龙头企业也曾出现过环保事故。但是这些龙头企业能够接受教训,意识到企业只有真正做到生产与环境友好,才能实现可持续发展,从而愿意投入大量资金进行技术研发和工艺改进。巨额环保投入非但没有让这些企业走上绝路,恰恰相反,让企业发展之路越走越宽,形成良性循环。
如何破解当前的环保难题,业内人士提出建议,应建立行业准入政策,对于新建鼓励类染料项目,要明确相应产品应达到的标准;政府部门应加强染料及中间体的环保设施验收管理,防止不具备环保处理能努力的企业在市场利润诱惑下,非法生产,出现市场不公平竞争;政府应颁布染料行业清洁生产标准,对已有或新建染料生产企业的生产规模、能耗、排污等进行约束,定期进行强制审核,建立落后产能淘汰制度,对列入国家“双高”产品、重污染工艺名录的,要制定淘汰产能的时间表。此外,也有专家表示,针对现在大部分南方染化企业迁至北方,国家应加大非法排污企业的查处力度,加强环保执法。同时,从扶持企业发展的角度出发,国家应该出台更多的政策和措施,比如在税收和信贷方面进行支持,鼓励和帮助那些有意识但没能力的企业完成环保升级。
而最根本的解决之道,还是营造环境保护的法治环境和社会环境。中国化学工业产能过剩由来已久,许多行业都处于低水平的竞争,这种长期的低水平的竞争无疑限制了技术的进步,延缓了对污染的治理,究其原因还是化工产业的环境门槛过低,企业环境违法成本过低是重要的原因,因此营造环境保护的法治环境和社会环境才是根本。
2014年,“依法治国”以前所未有的高度出现在党的十八届四中全会公报中,这充分说明了法律是最核心的制度安排,必须依靠法律来保护生态环境,依靠法律防治环境污染,提高环境质量。具体到行业层面,业内人士建议:一方面,政府要通过加大环保查处的力度来彰显法律的权威,震慑污染企业及其保护伞;另一方面,则是要加强公众和媒体的监督,公开企业排污的信息,通过透明度的增加使污染行为无处躲藏。从中国染料工业协会处了解到,信息公开制度是下一步行业将要建立起来的一项长效机制,染料行业未来将努力促使企业公开排污信息,接受来自舆论的监督。