、引言
独山子炼油厂300万t直馏柴油加氢氢气压缩机设备型号为2+1SVL320,机组类型为往复活塞式H型水平对置平衡型压缩机,制造厂家为德国诺曼埃索公司,是该厂关键设备。该压缩机为2007年12月新建300万t直馏柴油加氢装置新安装机组,共安装2台。其新氢段为2缸2级压缩,循环氢段为两缸单级压缩,工艺编号为K-101A、B,2011年9月对压缩机K-101B进行大修,拆检发现循环氢南缸靠近缸头侧活塞环断裂(见图1),其它缸活塞环棱角处有轻微的坑点,对该压缩机所有的活塞环进行更换。自检修后该压缩机运行五年来频繁出现新氢一级出口压力低故障,压缩机在运行过程中在靠近气缸缸体部位伴随有气流窜动的声音,进行拆检主要故障现象为活塞环、支撑环磨损严重、气缸粗糙度值变大。5年以来共对新氢一级缸活塞环磨损问题检修26次,加上其它故障,该压缩机平均运行周期不足2个月。由于运行周期短,给装置安全生产带来隐患,该问题亟待解决。通过对该压缩机维护管理升级及对故障原因进行逐一分析排查,最终通过对设备进行改造,解决了新氢缸一级出口压力低故障,延长了压缩机运行周期,确保装置平稳生产。
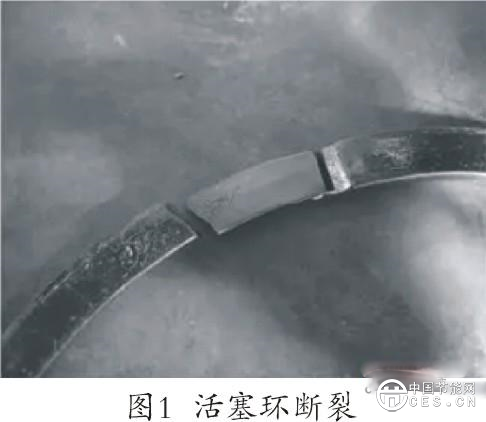
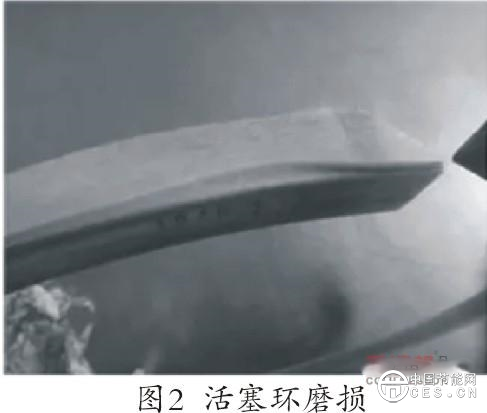
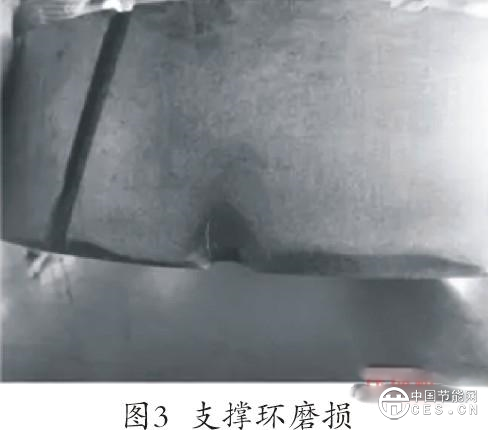
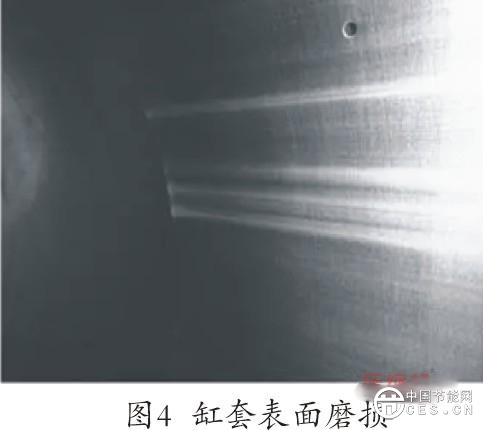
2、故障现象
通过对压缩机一级缸拆检查看故障现象为压缩机活塞环、支撑环均出现不同程度的磨损(见图2、图3),在活塞环及支撑环端面有气体吹蚀的痕迹,活塞环径向最大的磨损量在1.5~2.0mm范围内,支撑环径向最大磨损量在0.30~0.40mm范围内,气缸缸套表面运行一段时间后出现粗糙度磨损加剧的现象(见图4),原始缸套表面测量粗糙度为Ra0.5~0.6μm,磨损后现场实际测量粗糙度为Ra1.5~1.8μm,超过标准范围。
3、故障原因分析
3.1 活塞环、支撑环材质
300万K-101B压缩机在投用的初期,随机配件中有原压缩机厂家(诺曼埃索)生产的活塞环及支撑环,2011年9月更换原厂家配件,使用后运行周期较短。原厂家活塞环、支撑环材质均为聚四氟乙烯(PTFE),该材质的摩擦学性能随温度而变化,其中石墨能使PTFE基材料的摩擦系数减小,虽然本身耐磨性变差,但是对偶面磨损极小。分析认为原压缩机厂家活塞环、支撑环材质耐磨性差,后期通过和诺曼埃索厂家技术交流,建议使用PEEK材质的活塞环及支撑环,因为该材质较硬,耐磨性好。在2012年4月至2016年10月期间,先后试用了温州中大、沈阳远大压缩机厂、贺尔碧格等厂家生产的配件,这些厂家对活塞环及支撑环进行了材质升级及结构调整,通过填充不同的金属组份来提高活塞环及支撑环的强度、耐磨性。但是从使用效果来看都不是很好,压缩机运行一段时间后仍然出现新氢一级压力低、活塞环及支撑环磨损现象。
3.2 气缸缸套材质
300万K-101B压缩机随机安装的缸套材质为普通铸铁,2012年2月拆检测量新氢一、二级缸套表面粗糙度分别为Ra1.2μm、Ra1.5μm,已经超出压缩机检修规程SHS01020-2004所规定的压缩机缸套表面粗糙度一般值0.6μm。从缸套磨损的现象来看主要是表面有不规则的气体吹蚀的痕迹,分析认为气缸缸套材质耐磨性差,表面粗糙度加剧升高后,造成活塞环及支撑环磨损。2012年5月及9月先后更换了新氢缸一、二级气缸缸套,此次更换的缸套是由沈阳远大压缩机厂家生产,对缸套材质进行了升级,由原先的普通铸铁改为球墨铸铁。但是2013年11月该压缩机同样出现了新氢一级出口压力低现象,拆检气缸进行检查,发现活塞环、支撑环及缸套仍存在磨损。
3.3 活塞结构
该压缩机新氢一级活塞结构为组合式,是由两部分组成,通过超级螺母进行预紧连接,在靠近缸头活塞部位第一个活塞环槽内有一个直径为φ10mm 的小孔(见图5)。前期拆检压缩机进行检修过程中发现该孔边缘有被气体吹蚀的痕迹,并且靠近小孔的活塞环、支撑环吹蚀的都比较严重。分析认为压缩机在实际运行过程中,高速带压气体通过小孔对活塞环、支撑环及缸壁造成影响。
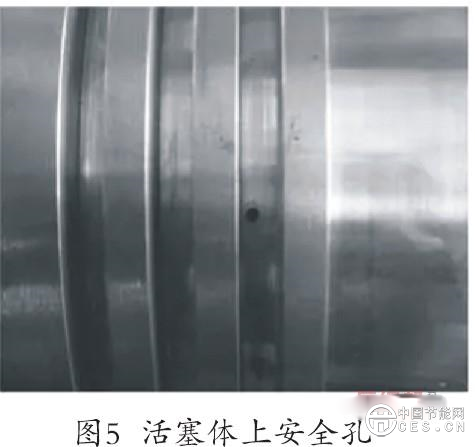
2012年4月对新氢缸一级活塞进行更换,并且使用焊接的办法堵住了小孔,试运机组一个月后同样又出现活塞环、支撑环磨损的现象。通过厂家了解到该小孔的设置可以保证活塞在实际的工作中端面的压力平衡,使得活塞端面不会产生变形,同时在活塞进行拆卸的过程中气体排出去后,方便检修人员对活塞进行拆卸,起到安全孔的作用。
3.4 活塞超级螺母预紧力
300万K-101B压缩机新氢缸一级活塞为组合式,通过M68mm的超级螺母进行预紧,在超级螺母四周均布12个M16的小螺母(见图6)。按照图纸上的要求,应先预紧固超级螺母,并且在超级螺母和活塞端面预留1~3mm间隙,然后开始对称紧固12个小螺栓,通过螺栓的拉伸从而紧固活塞。下面对现场实际预紧的螺栓紧力进行校核:
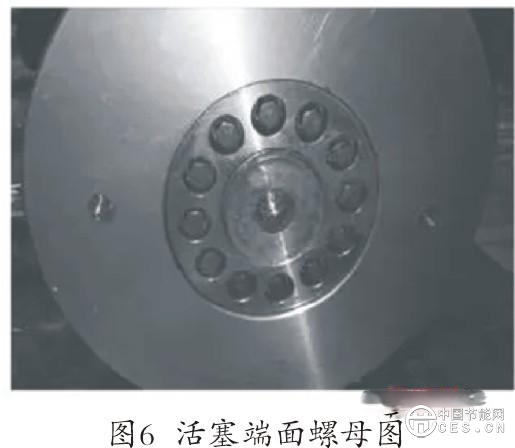
拧紧力矩=扭矩系数·预紧力·螺栓公称直径(1)
公式(1)中扭矩系数一般取0.11~0.15;预紧力按照图纸要求为975kN,按照公式(2)
F=K·R/Z·m·f (2)
其中K——可靠性系数,一般取1.1~1.3
Z——螺栓个数
f——结合面间的摩擦系数,一般取0.08
m——摩擦面的数量
F——每个螺栓所需的预紧力
R——横向载荷
因此作用在每个小螺母上的预紧力就是
F=1.2×975/12×12×0.08
=101.56 kN
螺纹的公称直径为M16,取D=0.016m
通过计算得
拧紧扭矩=0.13×101.56×0.012m
=160Nm≤192Nm
现场图纸要求紧固力矩为160Nm,可以根据现场实际需求,适当增大紧固力矩,但不能超过标注紧固力矩的120%,即为≤192Nm。因为扭矩系数的选取根据螺栓的实验数据所得,厂家在生产时没有将具体数值标注,所以只能通过估算选取中间值。如果现场紧固力矩小于160Nm,活塞在实际运行过程中就会在结合面存有间隙,压缩到气体通过该处间隙进入到活塞体,排气过程中再通过该处间隙和安全孔排出,这样活塞环就会由于密封比压失衡,失去密封作用,造成活塞环被吹蚀,加剧活塞环磨损。按要求检修过程紧固力矩定在180Nm,仍没有解决活塞环磨损问题。
3.5 注油量
通过对该压缩机润滑油进行分析,300万K-101B压缩机使用的润滑油为美孚威格力533,目前独山子炼油厂所有往复压缩机均使用此润滑油。厂家要求压缩机气缸注油量为11~15滴/min,现场新氢缸一级原先的注油头只有一个在十点钟方向,实际测量注油量满足使用要求,考虑到机组在实际运行过程中注油点只有一个会注油不均匀,因此现场在新氢缸一级缸头2点钟方向增加一个注油点,调整两个注油点的注油量为8~10滴/min,这样新氢缸一级缸头总的注油量就为16~20滴/min。通过检修拆检活塞组件可以看到,润滑油在活塞环及支撑环表面润滑均匀。前期和压缩机厂家技术人员进行交流,试图通过增大或减少注油量来验证活塞环及支撑环磨损的现象,但是效果都不是很理想,仍然会出现活塞环及支撑环磨损。
4、改造方案内容及具体措施
4.1方案论证
正常情况下,压缩机的活塞环和支承环寿命应该在6000h以上(常规介质,无油或少油工况),当压缩机的气缸出现正常磨损,或活塞环和支承环的材质有所改变,活塞环和支承环寿命可能有所降低,但绝对不会出现只能用一两天的异常状况。如果发生这种异常状况,一定是压缩机某个环节出现了严重问题。通过和沈阳远大压缩机厂技术人员交流分析认为,原机活塞环数列设计较少,24kg的压差分布在5个活塞环上(见图7),各个活塞环承受的径向压力(背压) 过大(尤其是最外端两侧的2个环),这是活塞环异常磨损的主要原因。由于支撑环和活塞环设计为斜切口,在压差作用下活塞环产生旋转属正常情况。根据国内压缩机设计的习惯及有关公司长期设计、改造氢气压缩机的经验,对比分析发现该压缩机活塞环数量偏少,易造成单个活塞环承受径向力过大出现磨损加剧。
活塞环的设计依据:材料和数量取决于压缩气体的种类和作用在活塞上的压差。活塞环设计基本原则(以空气为介质的经验公式):按密封压力差(单位kg)开平方,然后圆整。再根据润滑情况和气体特性适当调整。有油润滑活塞环可以适当少点,无油润滑适当增加;气体分子量大,容易密封,活塞环可以少点,气体分子量小,难于密封,数量必须增加。同等工况下,氢气压缩机的活塞环数量至少比空气压缩机增加50%,最好翻倍。
类似工况活塞环设计举例:60×104t/a馏分油加氢裂化装置新氢压缩机C-1002一级气缸工况:气缸直径:280mm;曲轴转速:300r/min;活塞行程:350mm;入口压力:2.4MPa;出口压力:5.96MPa;入口温度:40℃。该机活塞两侧差压3.5MPa,活塞环设计数量为6根。符合以空气为介质的经验公式。
4.2 改造实施
该压缩机一级出口压力降低后更换新活塞组件后效果立竿见影,解决活塞环密封效果差的核心问题是增加活塞环数量,降级各个活塞环的背压,进而减小其外圆周与气缸镜面间的磨损。
(1)原活塞体结构允许直接增加活塞环1根,两活塞环槽间隔约8mm,进行强度校核以及长周期运行条件评判,不建议在原活塞体上改造。根据测量校验采取在活塞体长度不变的情况下重新制作新活塞的方法,合理均匀布置活塞环,支撑环数列、宽度、厚度不做改改变,位置稍作调整,采用PTFE材料的活塞环根据改造活塞体具体尺寸重新设计制作。经过计算活塞在增设环槽后减小的质量对运行影响很小,因此改造方案确定执行。
(2)超级螺栓紧固力矩不够应该不是问题的主要原因,分体式活塞间的空腔可做密封处理。在活塞环槽底部约φ3mm的孔被堵的情况下,只需在分体活塞端面结合部位增设密封圈即可,防止气体窜动。
改造后的活塞组件结构与旧活塞组件不同点主要在以下几个方面:
(a)新活塞组件为6根活塞环,旧活塞组件为5根活塞环;
(b)新活塞环的位置在活塞上对称分布前后各3组,旧活塞环位置分布是活塞缸头侧为3组,曲轴侧为2组;
(c)支撑环位置新活塞组件在活塞中间布置,旧组件在活塞2个端面布置;
(d)新活塞组件没有设置安全孔,旧活塞组件在靠近缸头侧第一道活塞环槽内设置有安全孔;
(e)新活塞组件超级螺母有密封圈进行密封,旧活塞组件超级螺母没有密封设施。
5、实施效果
该压缩机自2016年10月份检修完毕后开机运行至今,现场状态监测机组运行平稳,一级缸出口压力稳定在4.61~4.71MPa之间,压比恒定在1.91~1.92之间,满足工艺生产需求,实现了长周期运行。文章中提到的故障分析及处理方法,希望能够给同类型往复压缩机的检修及故障分析提供借鉴。
6、结语
通过几年来在机动处、钳工车间及加氢联合车间的共同努力下解决了300万tK-101B压缩机新氢缸一级活塞坏及支撑环磨损的问题,期间对可能造成故障的原因进行逐一论证排查。每次故障数据进行认真分析总结,并且召开故障分析会,总结论证方案的可行性,这些数据的不断积累为后期设备改造及故障分析提供很好的数据支持,最终通过设备改造,解决了压缩机一级活塞环及支撑环磨损的原因,确保了关键机组长周期运行,实现装置平稳生产。